Scientific Research
Environmental impacts of storage tank fires, air pollution
In this chapter we will review the well-known facts by introducing the causes, the features, all the phenomena of extinguishing fires of different types of tank constructions (cone roof and floating roof) and finally the environmental impacts caused by these fires taking place mainly in the form of air pollution.
Measuring extinguishing procedures according to their environmental impacts
Fire fighting of different fire brigades can be examined similarly to those of the stationary technologies. We are given the subject of the work (the fire), the workers involved (firefighters) who do the necessary steps according to the prescribed technology. The product is the successfully extinguished fire. This activity involves using and effecting the environment as well as any other activities. The environmental effects greatly depend on the technology used in the process.
There are three basic traditional methods of fighting fires of tanks. All three have one feature in common tactical operating regulations include static intensity regulations, the prescribed intensity value does not depend on the size of fire surface.
Semi-fixed extinguishing strategy
After introducing the procedure in details, we will analyze its advantages and drawbacks, describe its implementation requirements, the regulations of the traditional application, the parameters, the environmental impacts of this strategy.
Environmental protection estimation:
Preparation time is long. Extinguishing runs long as a result of the low level of foam intensity, therefore burning time is considerable. As a consequence, air pollution is significant. Although foam pourers can drive foam inside the tank, due to their frequent breakdown fire brigade changed over to mobile fighting instead, but this can cause soil pollution by foam waste mounted on the tank as a result of aiming loss.
Operating with fixed extinguishing installation
Environmental estimation:
No need for preparation, the appliance carries out the fire fighting within a short time. Air pollution is relatively low, soil pollution does not occur in practice.
The method of mobile fire fighting
Today the traditional way of mobile fighting is carried out mainly in case of storage tanks with small sizes and the fires of dike areas and technological appliances.
The traditional mobile fighting should be separated from the application of high capacity foam guns and of mobile foam centres. High capacity foam guns in plants require different kind of resources (technical background, water, human being, mutual aid). The disadvantages include the costly technical appliances, the need for the required water supply of high pressure and capacity and due to the limited adaptability it cannot mean universal solution for all kinds of fires.
Environmental estimation:
The traditional way of fighting with the standard foam intensity results in long burning time and air pollution is high.
CONCLUSION
The traditional, most commonly used semi-fixed and mobile fire fighting apparatus work with static and low foam intensity rate, therefore the long burning time (that can even be increased by the time needed to install the apparatus and change the strategy) will result in considerable air pollution.
Possibilities of pollution prevention
Air pollution is in proportion to burning time and tank size. The possibilities of reducing burning time and air pollution:
.jpg)
How to reduce preparation time
Preparation time exclusively depends on the chosen extinguishing strategy. Based on the study of the elements of preparation time, actuating the fixed fire fighting apparatus requires the shortest time, extiguishing can start in a few seconds after detecting the fire. Adapting the semi-fixed or mobile fighting methods, detection, alarm, proceeding and assembly cause significant preparation time loss, firefighting can only start after having done these.
How to launch quick extinguishing procedure
- Using immediate physical heat sensors
- Using thermoplastic or melting pipes, bars, sheets (e.g.: pneumatic linear detector), appliances based on the technique of sprinkler heads installed on the upper rim of the sidewalls inside the tank or at the foam dam in tanks with floating roof
- Using electric heat-sensors (electric linear detectors)
- Using electric detectors perceiving heat radiation
- Using monitoring video systems based on veer-sensing software (scanning or immobile camcorder)
How to avoid false alarm
One of the most commonly used way of avoiding false alarm is after relying on the signal made by the perceivers, the operators supervise and check if it agrees with the facts.
Safety can be increased by rising the level of redundancy. Reducing the level of odds of false alarms can be reached by multiplying the detectors and reading their signals altogether in AND logical relationship.
How to reduce extinguishing time
According to our hypothesis, the solution can be found by examining the chart of extinguishing time and foam intensity. We prove the efficiency of extinguishing with FoamFatale™ meaning that fighting time can be drastically reduced by increasing the amount of foam solution.
The following chart shows the relationship between the foam solution intensity and the extinguishing time:
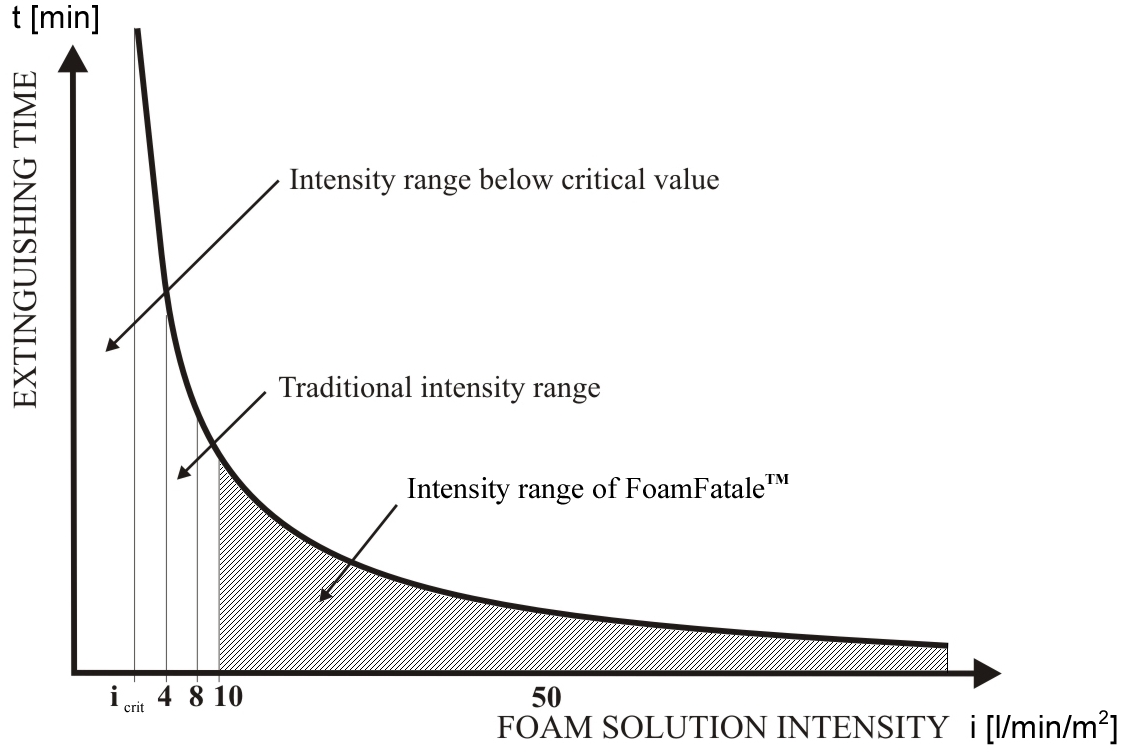
How to reduce soil pollution by reducing foam exploitation
Comparing extinguishing technologies
Pollution of above and underground water can be decreased by reducing the amount of extinguishing materials used and increasing the efficiency of their exploitation. Load of the sewage system can also be reduced by the foam amount used. The total amount of foam volume getting into the tank and into the dike area due to the aiming loss should be considered as pollution.
The rate of soil pollution depends on the foam exploitation of the certain technology as well as the method of foam introduction.
In order to be able to compare the different extinguishing technologies we introduce the concept and the standard of foam effectiveness factor. Defining its rate can be carried out by using easily adaptable evaluating methods. Having examined the relationship between the foam effectiveness factor and the foam intensity we realized that we can define the intensity of the optimal working point of certain extinguishing technology in concrete figures.
Based on theoretical assumptions the relationship between the foam exploitation factor and the foam solution intensity is depicted in the following chart:
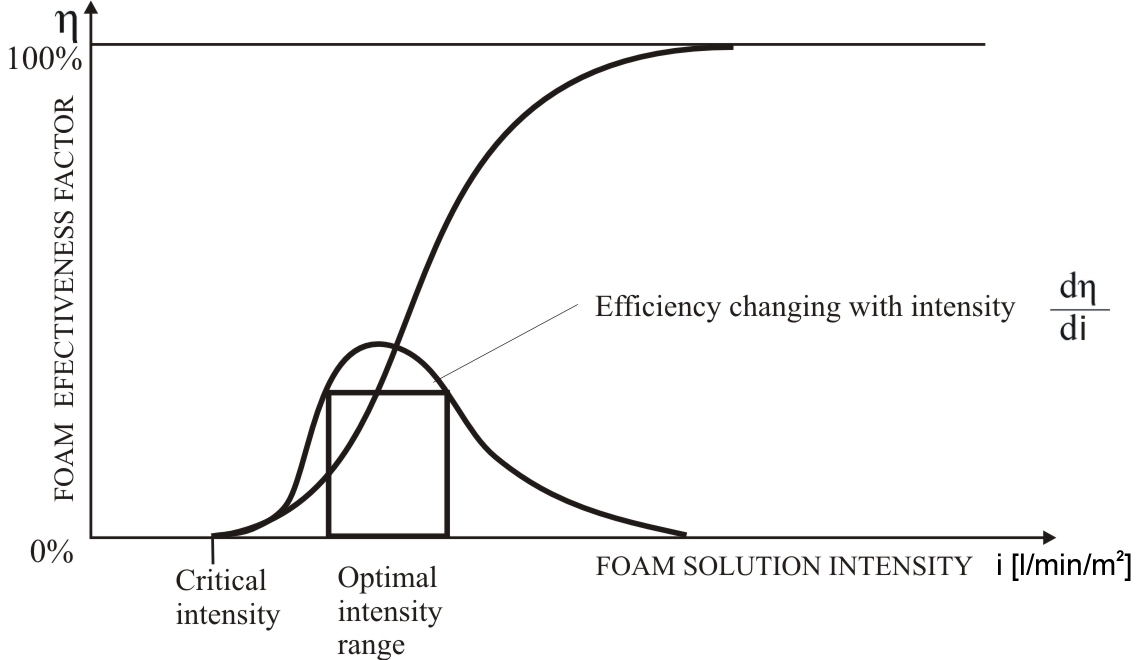
The value of η in case of less than critical foam solution intensity is 0, the fire could not be put out. In case of this low level of cumulative foam volume flow the penetrational speed decreases to 0 in view of the advanced time spending on putting out the fire and spreading of the foam face stops. The fire continuously consumes the released foam amount, t(extinguishing) = ∞
The value of η is 100% if the driven foam amount is used to create the foam blanket without any waste with its full volume. This case takes place in case of cold foam spreading experiments, providing the adaptation of high quality stable foam.
If we are aware of the relation between foam exploitation factor and solution intensity of different extinguishing strategies, before starting extinguishing the fire we can calculate the full foam volume to be produced in a certain case, moreover, the necessary foam concentrate amount taking the intensity into account resulting from the capacity of our technical background.
CONCLUSION
As a conclusion, we can state that fixed extinguishing equipment is favourable regarding preparation time.
The benefits of extinguishing with high capacity foam intensity should be exploited to reduce extinguishing time. The appropriate extinguishing strategy should be chosen by taking the best foam utilization factor into account and it should be operated in an optimal working point.
The technologies are characterized by their foam introduction manner. The most appropriate way among all the possible foam introductions is the curtain-like manner which is able to cool the inner part of the shell and stop wall-effect.
Based on these assumptions we developed a new extinguishing strategy of storage tank fires which adaptability were tested in an experimental way.
Hypothesis: introducing a new technology
Tactical instructions
As a ground principle of redefining tactical instructions we introduce the method of choosing the dynamic intensity in order to decrease burning time.
According to the foam solution intensity-extinguishing time diagram, above the value of 10 l/min/m2 intensity, in the range of FoamFatale™ system extinguishing time decreases rapidly. From a practical point of view, intensity value of 15 and 30 l/ min/m2 would be favourable in case of fixed and mobile extinguishing strategy.
The dynamic extinguishing strategy
We propose the working point should come in the intensity range of FoamFatale™ system in order to make air pollution small and to avoid harm caused by tank heat. In this case, based on our own measurements and the experiments of extinguishing fire by mobile strategy, extinguishing time drops to order magnitude of 10 seconds. This short extinguishing time should be favourable to keep in case of bigger fire surfaces and tank sizes.
According to the traditional tactical instructions, we were able to define the extinguishing time and the time of foam introduction reading the low intensity value from the extinguishing time-foam solution-intensity diagram. In order to obtain short extinguishing time we need to modify the extinguishing instructions regarding the time of foam introduction as the independent parameter, leaving the foam solution intensity the dependent variable and adjusting it to the size of the combustion surface.
In case of extinguishing, the first phase is to develop the necessary foam thickness for extinguishment. It requires a few 10 seconds in the range of FoamFatale™ system. The traditional, static approach prescribed the same intensity value independently from the combustion surface. Modifying this by instructing that the intensity value should be adjusted to the combustion surface, we can realize that in case of a bigger suface the foam should take a longer distance under the affection by the fire, the attacked foam surface gets bigger. The impacts of the inevitable foam destruction can be outweighed by increasing intensity and decreasing extinguishing time. With the help of an increased intensity value, the foam rolls faster on the surface, being exposed to the drying thermal demolishing impacts of fire for a short time of some 10 seconds.
The second phase of the extinguishing procedure is the increasing of the foam blanket thickness. Its importance lies in preventing reignition. We should continue the accession of the foam to the surface of the liquid until it grows up to an adequate thickness. We should be able to maintain the resistance of the foam blanket even if a strong sidewind tries to make the blanket go open. The bigger intensity value beside the fixed foam introduction time results in greater safety factor and the required bigger foam blanket thickness will be set by the end of the prescribed total foam introduction time.
Based on our measurements and the conclusions from calculating the foam spreading velocity to different tank size, we propose the following values of the diagram indicating the relation between the foam solution intensity and the fire surface.

In practice designing the extinguishing equipment consists of two steps, contrary to the traditional planning processes for example those working with statical intensity data from NFPA.
The first step is calculating the total foam amount needed and planning the capacity of the foam source. The method of foam supply is defined by the chosen extinguishing strategy. In case of fixed extinguishing equipment a fixed SEF® (which is a kind of pre-mixed, ready-to-use type foam), while in case of mobile extinguishing a mobile instant foam tank or high capacity mobile foam solution supply unit can be applied.
The second step is to plan the foam introduction, consisting of the hydraulic design of the foam pipe. The base of the design is the upper limit of foam introduction time. We should set it as a main criteria how much time we need to get the above defined total foam amount inside the tank on fire.
Based on our measurements and with the respect of the economically acceptable values resulting from examining the penetration velocity, we propose to introduce the following instructions:
The permissible longest foam introduction time at any size of tanks is maximum 2 minutes.
Based on the foam introduction time, we can calculate the foam volume rates in the foam pipes and as the next step, taking the equivalent pipe lengths into account, we can calculate the pipe cross sections.
The optimal way of foam introduction
In favour of fast extinguishing, foam application intensity should be increased. In order to achieve this, extensive foam volume rate should be introduced to the tank on fire. Traditional foam chambers, foam slides are not suitable for managing this extensive foam volume rate, since the foam is introduced pointwisely with high velocity, it raises the hydrocarbon surface in landing, the foam submerges into the liquid creating emulsion and the high paced floods hardly develop a cool vapour proof foam blanket.
The appropriate choice of foam introduction can improve the efficiency of the extinguishing in two fields. We can benefit from the environmental asset preventing soil pollution by driving the total foam amount to the tank without any waste. In addition to this, we can obtain the best foam exploitation factor, which is most important concerning the reduction of total foam amount used.
To be able to find the most favourable way of foam introduction, we carried out theoretical research of the examination of penetration velocity, foam profile diagram, foam perimeter curve and the geometrical possibilities of foam introduction.
We discovered the theoretical and the physical explanation of the so-called wall-effect phenomenon and its related anomalies. In the meantime, we applied the specific surface foam load attribute number as one of the parameters of the extinction.
Having studied the different foam introduction geometrical schemes, the curtain-like foam streaming inside the tank shield was the most promising. Its equipment is the Continuous Linear Nozzle.
Foam supplying solutions suitable for extensive foam intensity
There are three solutions perfect in practical usage to feed the Continuous Linear Nozzle with the necessary foam volume flood. The first two are based on the application of Self-Expanding Foam attaining the autonomous extinguishing equipment free of any external sources.
Fixed foam supply system with Self-Expanding Foam:
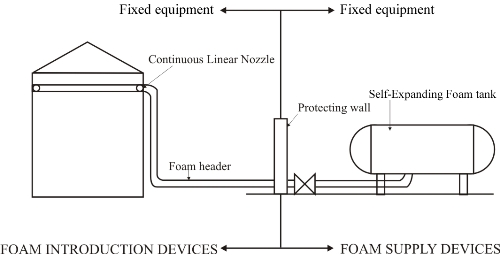
Mobile foam supply with instant foam from tank truck:
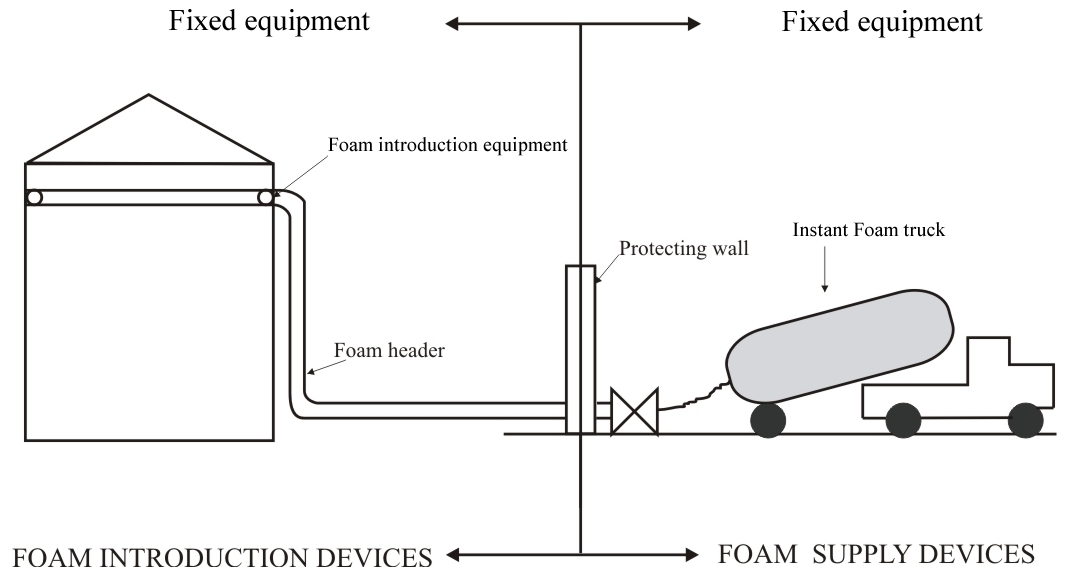
Mobile foam supply updated semi-fixed extinguishing equipment
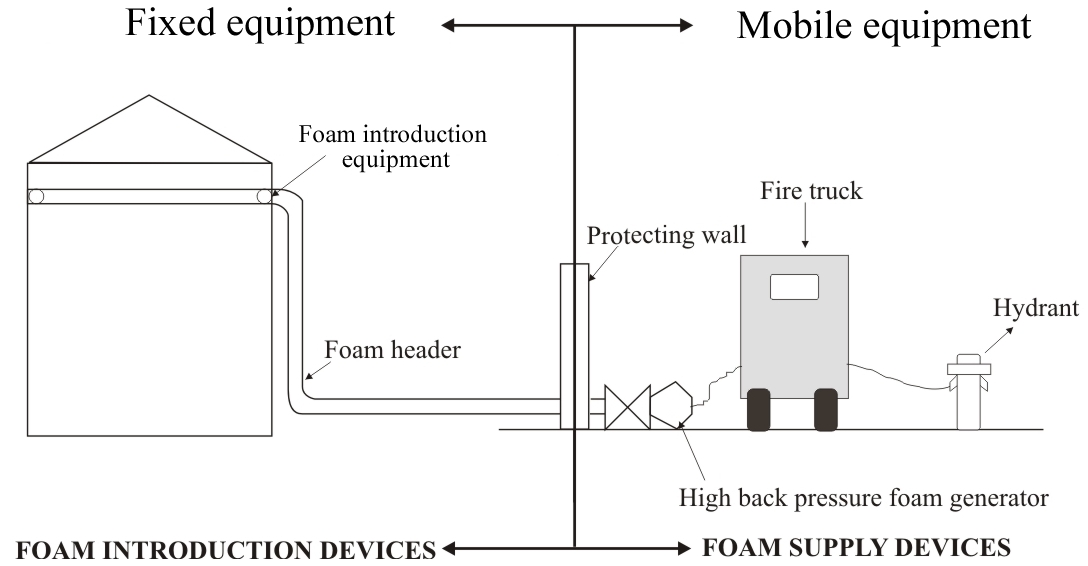
The features and the applied equipment at the three foam supply systems are summarized below.
.jpg)
Experimental evidences on theoretical results
So far we have outlined the different phases of our research work:
- How to reduce preparation and extinguishing time along with air pollution by increasing the foam application intensity
- How to prevent soil pollution, how to manage extensive foam volume rates properly and drive it to the tank
- How to produce adequate amount of foam in different fire extinguishing strategies
- How to avoid false alarm
In the next chapter we will prove all of our theoretical results by experimental evidence of cold foam spreading measurements and fire tests.
Cold foam spread tests
We built an opened tank model with 500 m2 surface, made of steel sheets to be able to carry out our measurements. All results of the measurements are included in the following charts.
Chart of the issues of cold foam tests are based on the report of Ministry of Interior National Catastrophe Defence Directorate, Fire Test Laboratory.
.jpg)
We carried out the foam spreading experiments with nearly the same extinguishing parameters partly due to the experimental equipment, partly to the bound feature of the foam sources. In every case less than half a minute was needed to reach foam closing, which can be regarded a significant achievement, it also brings some hope for the future to reach a similarly short extinguishing time.
Another accomplishment is to comply with all the criteria of FoamFatale™ by mobile foam supply.
Fire tests
The change of the penetration velocity when foam is exposed to fire was considered important. We carried out two fire tests and compared the results with the measured parameters in cold conditions.
Chart of the issues of cold foam tests are based on the report of Ministry of Interior National Catastrophe Defence Directorate, Fire Test Laboratory.
.jpg)
Evaluation of measured results
There was a significant difference concerning the circumstances of the two fire tests that we did and unfortunately we failed to draw our attention to it until the beginning of the second test.
The water in the tank model had been left contaminated from the time the previous test was taken. As a result of this, 3-5 mm thick alga crust generated on the surface of the water and it was floating. Unfortunately, the drawbacks of the phenomenon were recognized later, after watching the video recording. Apparently, during the filling of the flammable liquid from the tank truck, the alga crust was broken by the mixture of petrol and pushed ahead. So the relatively longer extinguishing time can be attributed to the alga pollution in the second test. During extinguishing, the presumedly burnt and stiffened alga mass could hinder the spreading of the foam, decreasing the penetration velocity and towards the end of the whole process the alga drenched in petrol was accumulated in front of the foam, in the middle of the liquid surface and was burning for a long time like a wick in a candle. Eventually, the foam covered this last piece of burning surface, but caused the extinguishing time to increase a little bit.
CONCLUSION
- There is no measurable foam waste at 15 l/min/m2 foam solution application rateapplied on a 500 m2 experimental tank model. The foam closing time is about the same, 30 seconds at cold foam spread test and at fire test as well.
- The floating and flammable firm contamination on the liquid surface did not risk, but delayed the successful outcome of putting out the fire.
- The results serve as evidence of our hypothesis, the large tank fire surfaces will be extinguished using the appropriate increased intensity range.